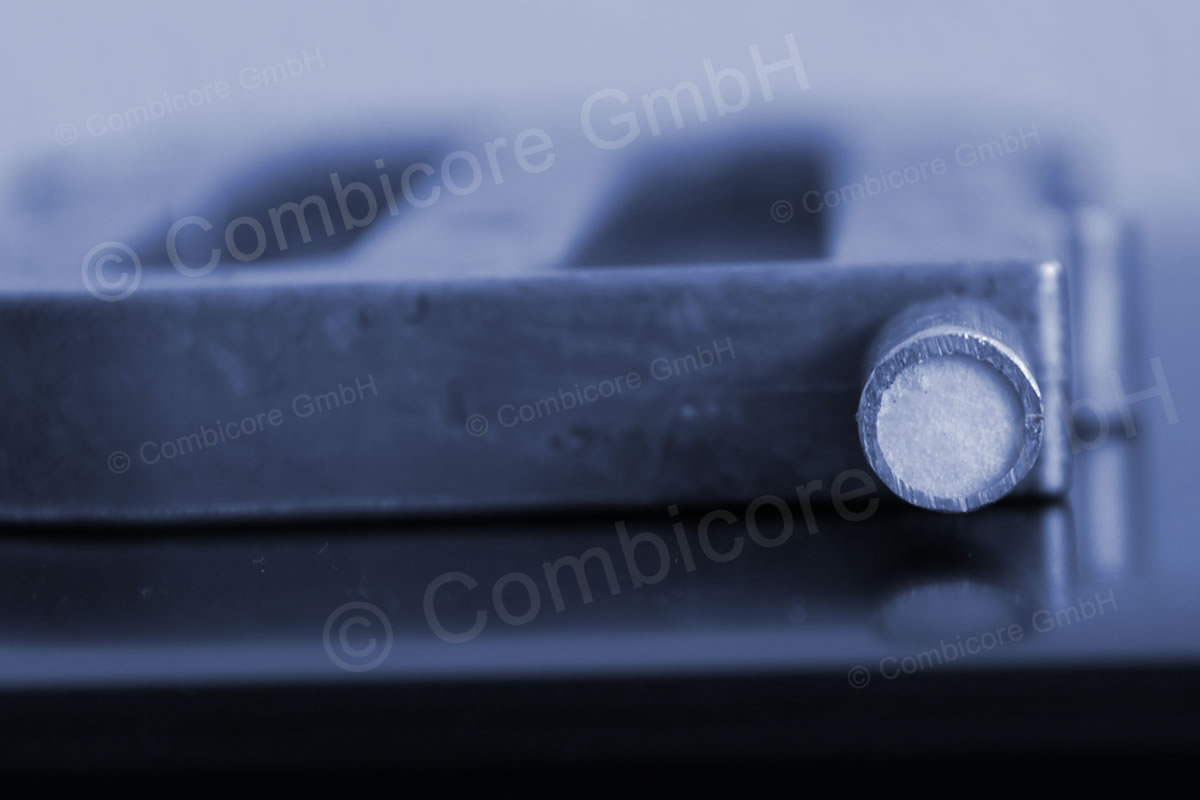
Loading...
Channels and other cavities in cast parts are needed for different function, like cooling, for lubrication or just to get a lighter part. Normally such channels are drilled, realized with feaders or different plates glued together. Sand cores are not usable in high pressure die casting (HPDC) with casting pressures over 1000 bar.
The Combicore technology builds up a compact package of core solutions. The basis of our core technology is a shaped metal shell that is filled with a special material. Combicore cores are extremely stable and can also be used in high pressure die casting with casting pressures over 1200 bar. After the casting process, the filling is removed. The metal shell remains as a leakage-free channel in the component.
Combicore cores offer valuable solutions for all casting processes and support efficient lightweight designs.
Typical automotive applications are heat sinks, cooling plates, battery housings, DC / DC converters, electric motors,...
Typical automotive applications are heat sinks, cooling plates, battery housings, DC / DC converters, electric motors,...
Combicore properties offer decisive success criteria:
The Combicore cores enables foundries to create media-carrying channels and other cavities in cast parts, efficiently, quickly, reliably and cost-effectively. The following dimensions and guidelines are common. Other materials are possible and we support you in finding the best solution for your challenges.
Alloys: | AlMn1 / EN AW 3103, AlMgSi0,5 / EN AW 6060, Al99,5 / EN AW 1050, CW021A / CU-HCP / 2.0070, CW024A / CU-DHP / 2.0090, E195, E235, 1.4301, etc. |
Channel-Ø: | from 0,5 mm |
Wall thickness metal casing: | from 0,5 mm |
Channel length: | several meters possible |
The Combicore technology creates highly efficient cooling channels, which ensure optimal temperature control of the near-net-shape cast part. Lubrication channels are also typical applications in the automotive sector.
With Combicore, casting cores are used in high pressure die casting for the first time.
Trust in our decades of experience.
As an innovation, Combicore cores and components from our customers have received multiple recognitions.
In recent years, the Combicore technology has received several awards and has been recognized as innovative and particularly sustainable. We present a small selection of our most important "achievements" here.
The Certificate Office for Research Allowance (BSFZ) of the German Federal Ministry of Education and Research confirms our great innovative competence also this year. We are very happy about that. We will present the results of our research activities to you soon. Don't want to wait? Then get in touch with us now. Let's realize ideas and innovations together!
Combicore has been awarded the industry prize four times in a row. We are Best of in the categories Automotive and supplier. Our innovative core solution for foundries convinced the top-class jury of experts. Our technology is of very high technical, economic, ecological and social benefit. We see the award as confirmation of our conviction that we work in a solution-oriented manner and thus meet the demands of our customers, namely to always be one step ahead. We have not participated since award winners were asked to plan an advertising budget.
The heat sink for a cooling plate in hybrid technology from the Moneva foundry received special recognition. The jury from research and science praised the strong innovative strength and high demands in casting technology.
The die-cast insert is an important pioneer for the use of hybrid drives, according to the jury. Sophisticated cooling technology solves problems in battery technology. The product-safe cast aluminum cooling tube in a secondary aluminum alloy is important for the recognition. The substitution of the multi-part sheet metal construction leads to significant cost savings.
The heat sink accommodates the lithium-ion cells and ensures that the temperature of the battery pack is even.
That was in 2012. We are particularly proud of this award and with this application we were among the first automotive suppliers for new technologies in electromobility.
The German Material Efficiency Prize was awarded to us by the Federal Ministry of Economics and Technology (BMWi) in Berlin in 2010. Since then we have continuously developed our technology. Even then, people recognized our creative and innovative ideas in the field of foundry technology.
"Those who produce efficiently win!" Emphasized Jochen Homann, State Secretary in the BMWi. Material efficiency pays off after a short time. With intelligent solutions, raw and operational materials can be saved in the long term. "That creates clear competitive advantages," says Homann.
In the same year we prevailed against 420 applicants from 23 countries and were named Innovation Champion by the Network of Automotive Excellence (NoAE).